Understanding Plastic Injection Molding Manufacturers: The Backbone of Modern Manufacturing
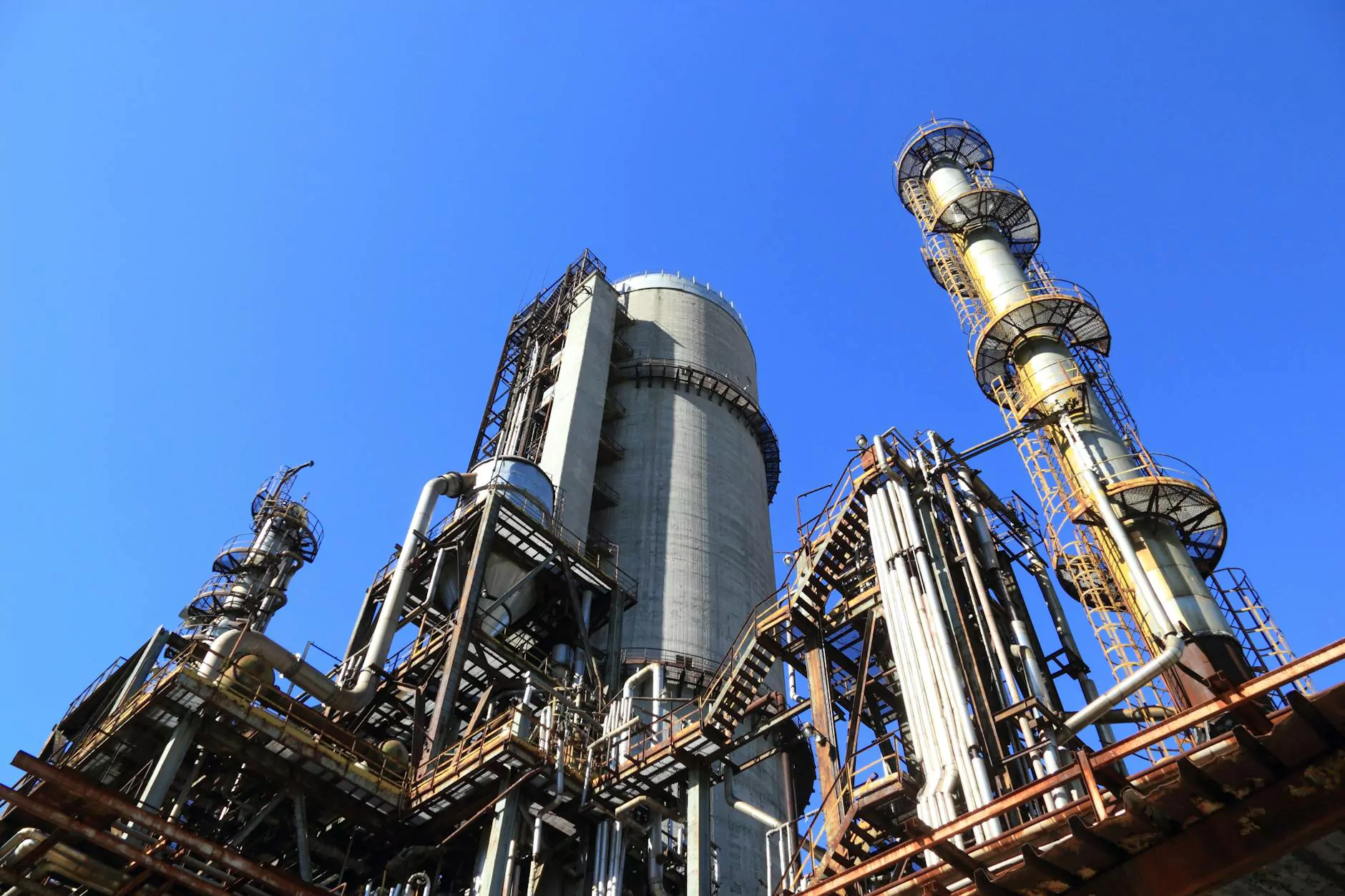
The plastic injection molding manufacturers industry plays a crucial role in today's manufacturing landscape. This process is not only essential for producing plastic parts efficiently, but it also drives innovation across various sectors. In this comprehensive article, we will delve deeper into the realm of plastic injection molding, exploring its advantages, applications, and the key players within the industry.
The Process of Plastic Injection Molding
At its core, the plastic injection molding process involves the production of parts by injecting molten plastic into a mold. This method is favored for its ability to create complex shapes with high precision and minimal waste. Here is a detailed breakdown of the steps involved in the plastic injection molding process:
- Material Selection: The first step involves choosing the appropriate plastic materials, which can include thermoplastics, thermosetting polymers, and elastomers.
- Mold Design: After material selection, the design of the mold takes place. This requires specialized knowledge to ensure that the mold can withstand high pressures and temperatures.
- Injection: The machine heats the selected plastic until it becomes molten and then injects it into the mold under high pressure.
- Cooling and Solidification: Once injected, the plastic is allowed to cool and solidify in the mold, forming the desired part.
- Mold Release: After cooling, the mold opens, and the finished part is ejected.
- Finishing: The final step often involves post-processing operations such as trimming and surface finishing to ensure high quality.
Advantages of Plastic Injection Molding
The popularity of plastic injection molding is attributed to a multitude of advantages that it offers to manufacturers. Here are some key benefits:
- High Efficiency: Once set up, injection molding can produce large quantities of identical parts quickly.
- Precision and Consistency: This method allows for tight tolerances and high variability, ensuring that every part meets the required specifications.
- Cost-Effectiveness: Reducing waste and optimizing material use makes injection molding a cost-efficient process, especially for large runs.
- Versatility: It accommodates a wide range of materials and can produce complex shapes that would be difficult or impossible with other methods.
- Environmental Benefits: Recycling of plastic materials and decreased waste management costs make it a more environmentally friendly option.
Applications of Plastic Injection Molding
The scope of applications for plastic injection molded products is vast and spans several industries. Below are some of the most common applications:
1. Automotive Industry
In the automotive sector, plastic injection molding manufacturers produce a variety of components such as dashboards, door panels, and clips that are essential for vehicle assembly. Using injection molded plastic reduces weight and enhances fuel efficiency.
2. Consumer Products
From household items to electronics, plastic injection molded products are prevalent. This includes everything from bottles and containers to more complex electronic housings that require detailed designs.
3. Medical Devices
The medical industry benefits immensely from plastic injection molding as it allows for the production of intricate medical devices and disposable supplies. Ensuring hygiene and precision is crucial in this sector.
4. Packaging Solutions
Plastic injection molding plays a vital role in creating packaging materials that are not only durable but also lightweight. These materials are essential for shipping and storage across various industries.
5. Industrial Applications
Many industrial components, such as machinery parts and tools, rely on plastic injection molding to create effective and durable products that can withstand intense working conditions.
Choosing the Right Plastic Injection Molding Manufacturer
With numerous plastic injection molding manufacturers available, selecting the right one can be a daunting task. Here are some factors to consider when making your choice:
1. Experience and Expertise
Look for manufacturers with a proven track record and specific experience in your industry. Their expertise can save time and reduce errors.
2. Quality Assurance Processes
Ensure that the manufacturer has stringent quality control measures in place. This includes regular inspections and testing of products to meet industry standards.
3. Technology and Equipment
The latest technology enhances efficiency and quality. Confirm that the manufacturer invests in modern equipment and stays updated on industry advancements.
4. Customer Support
Excellent customer support can help streamline communication and address any concerns quickly. A responsive manufacturer can significantly enhance your experience.
5. Sustainability Practices
With an increasing focus on sustainability, it’s essential to partner with manufacturers who prioritize eco-friendly practices and materials.
The Future of Plastic Injection Molding
As we move forward, the plastic injection molding industry is poised for tremendous growth and innovation. Some key trends and developments to watch for include:
1. Advancements in Materials
New polymers and composites that offer improved performance and sustainability are being developed, expanding the capabilities of injection molding.
2. Automation and Industry 4.0
Incorporation of automation and IoT (Internet of Things) technologies is increasing efficiency and reducing costs in the production process.
3. Customization
With the rise of consumer demands for customization, manufacturers are leveraging injection molding to create tailored products that meet specific client needs.
4. Environmental Regulations
As regulations become stricter regarding plastic use and waste, manufacturers must adapt by innovating products that are either recyclable or biodegradable.
5. Global Trade Dynamics
Shifts in global trade policies could influence sourcing and manufacturing strategies. Manufacturers need to remain agile to respond to these changes effectively.
Conclusion
In conclusion, plastic injection molding manufacturers are a cornerstone of modern manufacturing, offering efficiency, precision, and versatility across numerous industries. By understanding the process, advantages, applications, and future trends, businesses can make informed decisions when partnering with manufacturers. As technology continues to evolve, those within the industry must embrace innovation and sustainability to thrive in a competitive landscape.
For more information on high-quality plastic injection molding, contact us at Deep Mould – we are dedicated to providing exceptional services tailored to your business needs.